Model | HB400X |
Machine Body | X/Y Travel | 400×300mm |
Electrode wire diameter | φ 0.10-φ0.25 mm |
Wire speed | 1.18-11.8 m/s |
Net weight / gross weight | 1900 kg/2500 kg |
Machine dimension | L2020x W1700mm |
Workpiece | Max. cutting thickness | 300mm |
Max. cutting taper | ±10°/ 100mm |
Max. workpiece size | 930mm*550mm*300mm |
Max. workpiece weight | 500kgs |
Working Fluid Tank | Filtration accuracy | 0.01mm |
Capacity | 130L |
Working Method | Multiple filtration system |
Pulse Power Supply | Max. Cutting Speed | ≥300mm²/min |
Best Surface Finish | Ra≤0.4μm |
Max.Current | 12A |
CNC Power Supply Unit system | Hardware Configurations | Linear Motor, Full-closed grating scale, Import frequency converter |
Connecting Port | USB, LAN |
Program Code | ISO Code |
Axis Numbers | 4-axis Simultaneous Control, Realizing pitch compensation |
Joy Stick | Standard |
Language | Chinese, English, Korean, Japanese |
Aluminum Machining | Option |
Titanium Machining | Standard |
Z axis numerical control | Standard |
Power Supply | Power | 3~380V+10% 50±10Hz |
Environment Temperature | 10~35℃ |
Power Consumption | 1.5 KVA |
Best Surface Roughness ≤Ra0.4μm
Maximum Efficiency Up To 300mm²/min
Nonelectrolyte Power Supply Technology
Four axes(X,Y,U,V) AC Servo combined with four axes imported ball screw and liner guideway,which guarantee the accurate.
‘
Independent Layout of X axis and Y axis, With UV…. to ensure the high accurate. Thick-walled castings with Stiffener configuration avoids the body deformations.
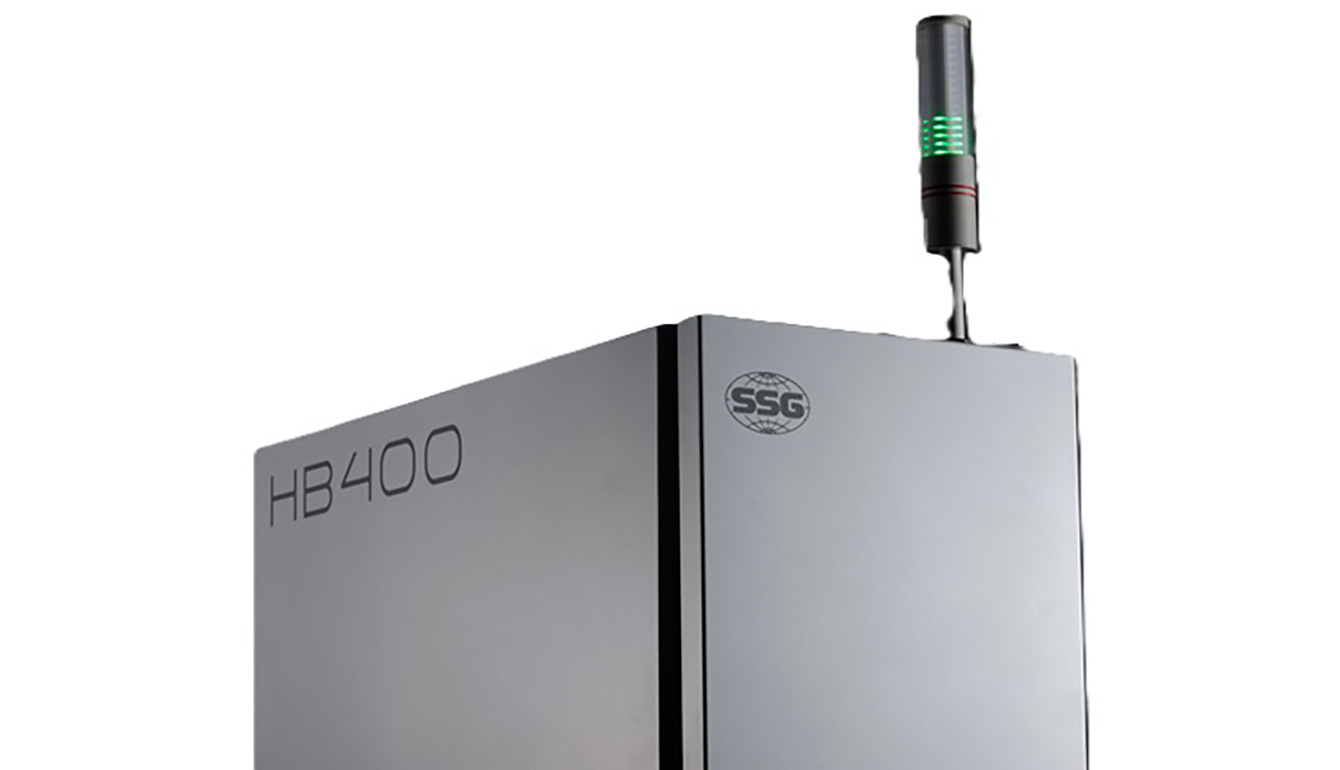

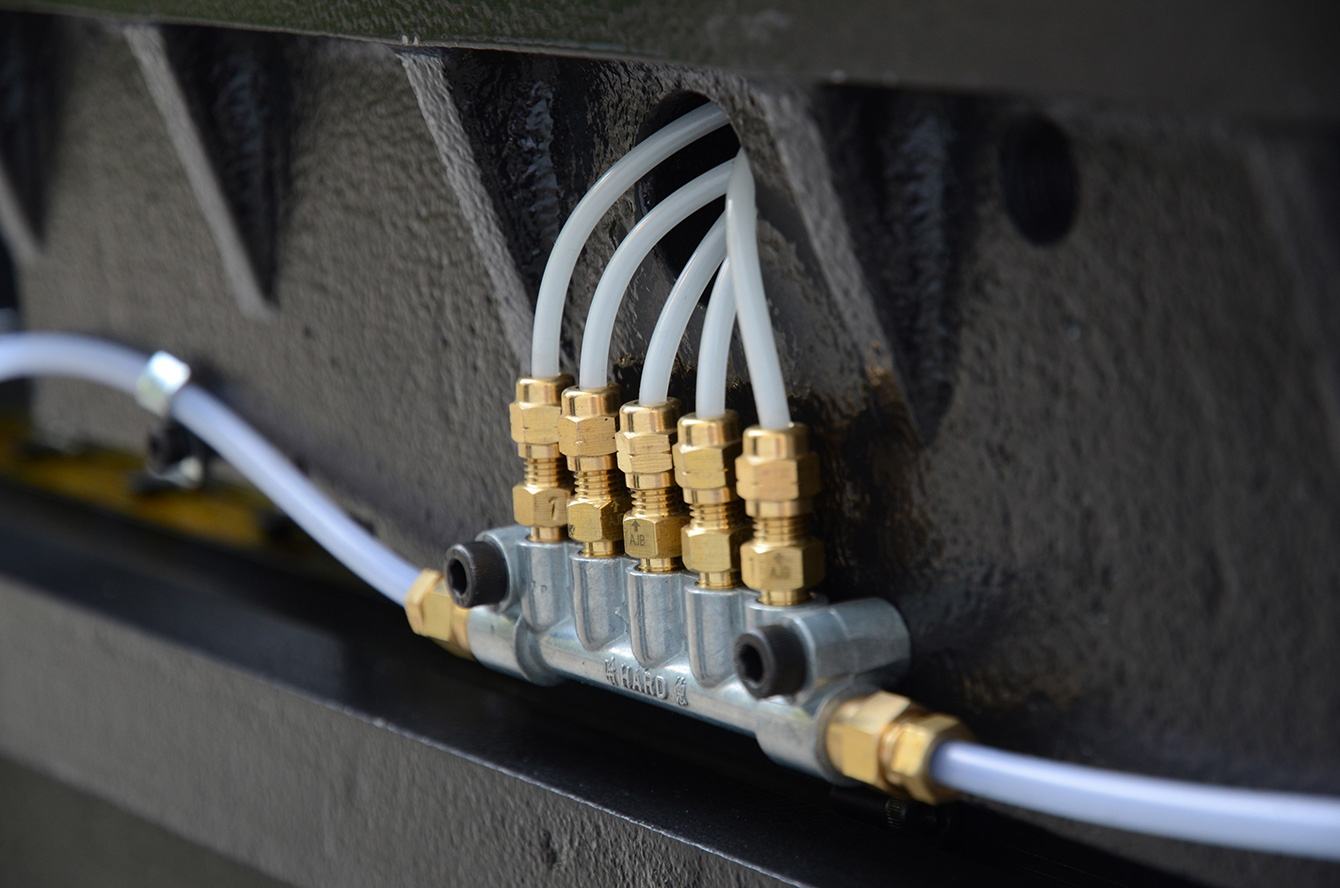
-
Imported AC servo system helps cutting speed faster and precision higher
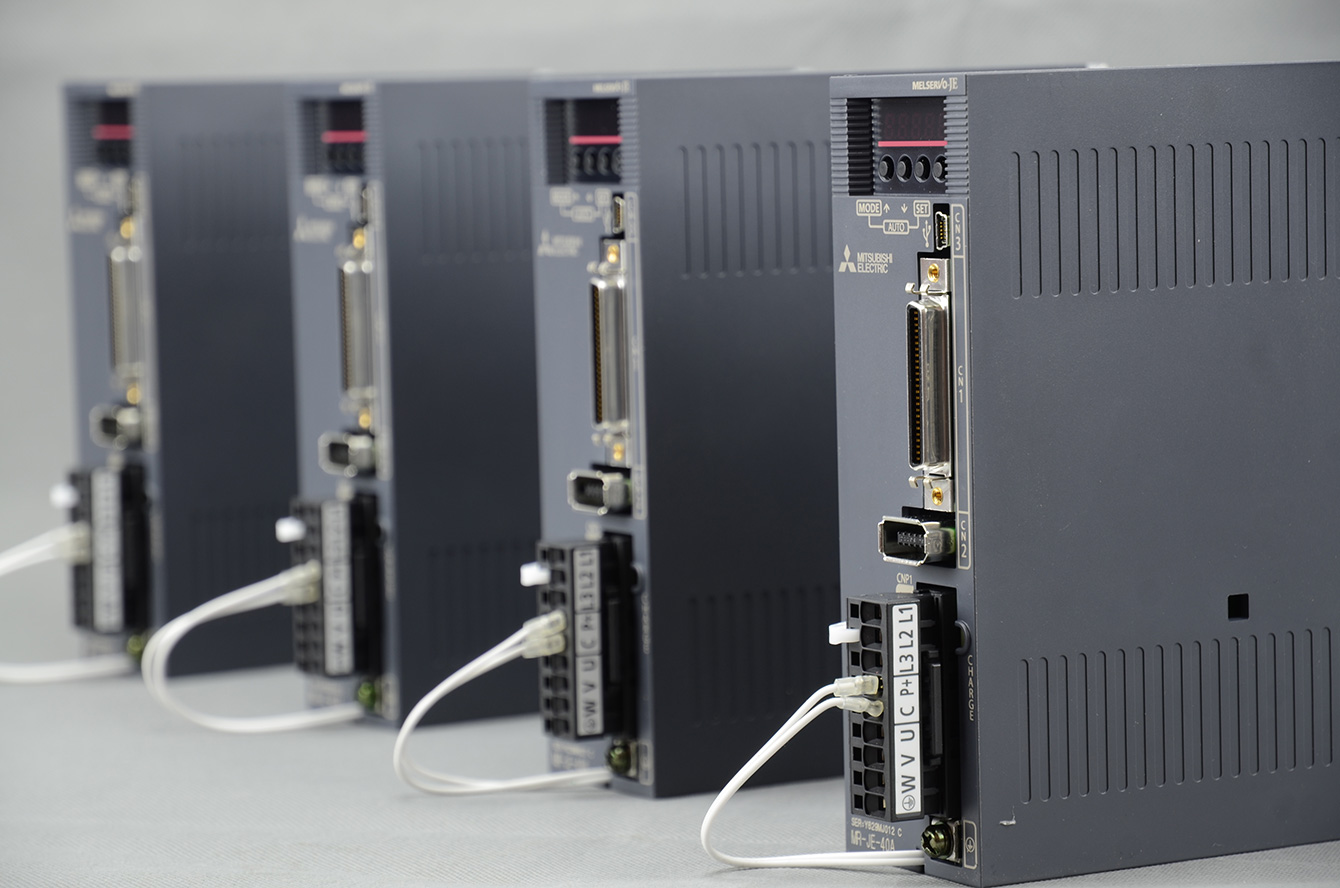
Operation System
Built-in programming graphics and automatically prepared machining code programs. The multi-CPU function enables simultaneous processing and programming.
Parallel compensation, clear angle setting, program image, corner optimization, scaling and other functions opened.
Laser ranging calibration and pitch compensation data opening real-time on.
Multiple coordinate system can switch among workpieces rapidly.
Exchange X and Y axis randomly to adapt different machining state. Set wire controller's move speed freely.
Record machining tracking information, to monitor machining during unmanned operation to ensure safety.
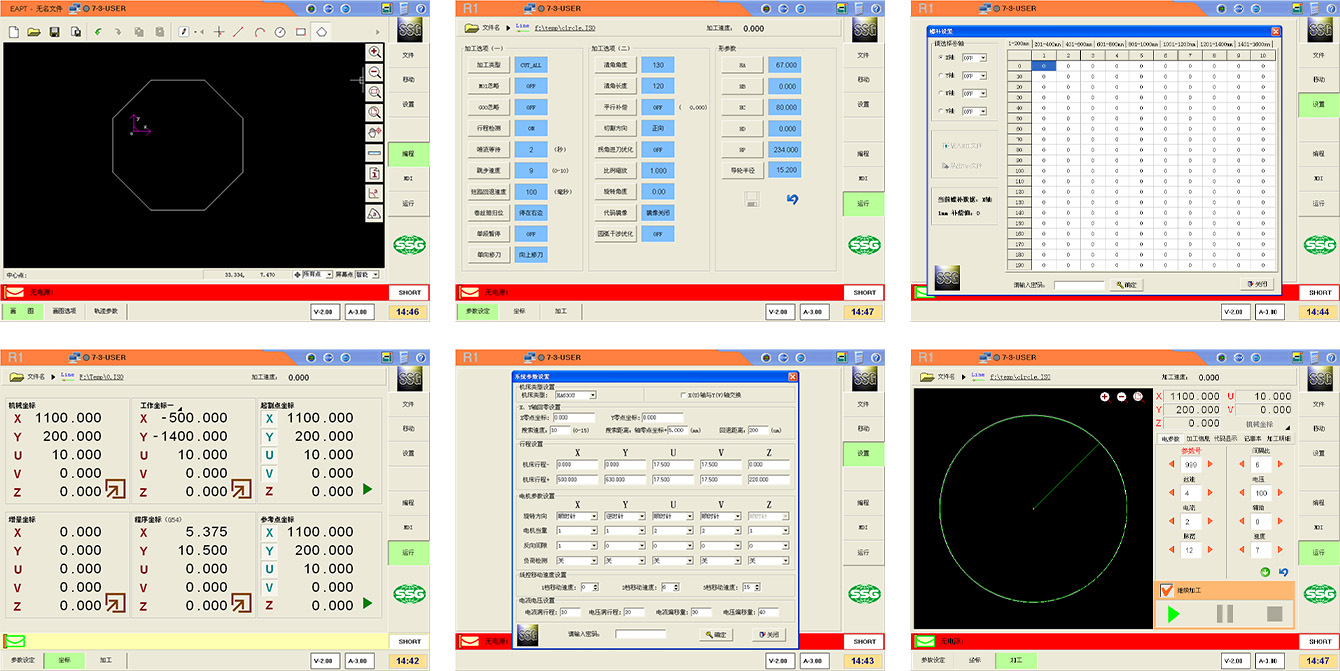